Overcoming manufacturing capacity, capability, and cost constraints
By Chris Brumitt, Managing Director, Aerospace & Defense
The constraints that manufacturers face come from multiple external and internal sources. While manufacturers can work together to comply with regulatory, political, and other external constraints, each manufacturer must work individually to overcome their specific internal capacity, capability, and cost constraints; and if done successfully, this multi-functional pursuit provides a competitive edge. This blog draws on the insights gained from helping design and manufacturing companies address a number of significant production constraints.
In a recent case, the production readiness initiatives assessment undertaken at an aerospace composites manufacturer is positioning it to identify and attack the cause of high overrun costs, excessive waste, and inefficient use of space, as well as reducing the cost and delays associated with nonconforming parts. The company has an opportunity to reduce up to 11,650 hours over multiple workstreams and has identified future initiatives that would allow it to handle a projected tripling in demand over the next two to three years.
These results are based in a multi-faceted approach to overcoming manufacturing constraints: diving deeply into processes for a root cause analysis of delays and bottlenecks; implementing the right visibility and management tools; optimizing the manufacturing footprint and network to increase capacity; and creating a culture of continuous improvement.
Root Cause Analysis
To determine the root causes of bottlenecks and other constraints requires examining work processes in depth. Process mapping, day-in-the-life-of (DILO) studies, surveys, benchmarking, interviews across the functional organizations, and value stream mapping creates a clear understanding about capacity and capability constraints, including under- or over-utilization of equipment, balanced resource utilization, and gaps in workforce skills.
As a result of a root cause analysis, the aerospace composites manufacturer established a framework to address:
- Standard work instructions
- Improved KPIs related to company goals
- Preventive maintenance, leading to less downtime and improved OEE
- Total value optimization (TVO) to raise the maturity of operations and production
- A method for evaluating future initiatives based on ease of implementation, capital cost, likelihood of major improvement, and training to drive long-term sustainability
Visibility and Management Tools
A manufacturing company’s systems continually evolve in order to keep up with changing business dynamics, and maximize utilization of new technologies. As a result, important data is collected but is often locked into misaligned systems and not visible in a form that leaders understand and trust. This lack of visibility means decision making is frequently reactive and not predictive. For example, leaders may struggle to make critical decisions such as CapEx and footprint optimization due to incomplete data.
In addition, as the workforce changes—key employees retire and new employees join—legacy knowledge about processes, systems, and techniques may be lost or become irrelevant. Productivity may be affected due to a lack of processes and best practices which further reduces efficiency.
Visibility and management tools like the following help to overcome these constraints:
- Master resource schedule and other scheduling tools
- Sales, inventory, and operations planning (SIOP)
- Predictive and preventive maintenance processes
- Digital work instructions and Visual Management Boards
- Warehouse and other tracking systems
Footprint and Network Optimization
Footprint optimization can increase productivity, shipping and loading, and throughput with such improvements as placing resources closer to the production area, redesigning sorting and pick production zones, and closing the communication gap between procurement, operations, and inventory. Network optimization makes logistics more efficient to reduce demurrage costs, ensure that supplies are available when and where needed, and improve customer satisfaction.
Constraints on the footprint and network design may lead to an imbalance of supply and demand, costly overdependence on 3PL suppliers, and nonconformance of parts that exasperates customers and causes excessive waste. To avoid these problems through footprint and network optimization, a company needs to:
- Calculate a realistic cost to serve, including both direct and indirect spend
- Strengthen and shorten the supply line with a combination of in-shore, on-shore, and off-shore suppliers
- Analyze the company’s make vs. buy identity
- Analyze overall equipment effectiveness (OEE) to track uptime, maintenance, and accuracy
- Gather pallet and SKU information to track locations and ensure transparency.
Culture of Continuous Improvement
The aerospace composites manufacturer faced the problem of hidden factories that operated within the facility but outside normal operations and with little oversight. This problem was one of several factors leading to a lack of uniformly communicated KPIs, clear work instructions, and a culture of problem solving rather than finger pointing.
When the entire plan-buy-make-move supply chain operates in concert and at the same level of maturity, a company reaps the benefits of follow-through on initiatives, an atmosphere of continuous improvement, and the elimination of silos. With improved communication comes more trustworthy and timely data, giving the C-suite more control over outcomes and more ability to address capacity, cost, and capability constraints before they escalate.
To develop a culture of continuous improvement, a company should build on the information revealed from root cause analysis and build a robust Management Operating System (MOS) to drive accountability through:
- Owner, responsible, consult, and inform (ORCI) roles
- Leadership and organization improvement
- Standard operating procedures
- Management operating systems
- Skills and oversight training.
Conclusion
Manufacturers face multiple constraints involving physical space, availability of equipment, labor shortages, outdated technology and skill sets, rising raw material and labor costs, difficulty in meeting regulations, demand variability, and competition for customers and raw materials. Through root cause analysis, the use of visibility and management tools, footprint and network optimization, and a culture of continuous improvement, manufacturers can better identify, control, and mitigate these capacity, capability and cost constraints, not only in the immediate future but for long term progress, which leads to improved production readiness, EBITDA, and profits.
To read the full case study discussed in this blog, click here.
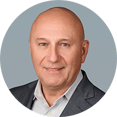