A new lens for optimizing multimillion-dollar decisions
As a leader making multimillion-dollar decisions, you need complete confidence in:
- The quality, timeliness, and reliability of data for planning and forecasting
- The completeness of your 360 degree view of the end-to-end supply chain
- The ability of your company to adapt to a volatile, uncertain, complex, and ambiguous (VUCA) marketplace
- Your control over change and innovation.
SGS Maine Pointe has developed a new lens for optimizing decision making across the end-to-end supply chain. Our integrated strategy incorporates Design for Excellence (DfX), SIOP, optionality, advanced analytics & simulation, and ESG.
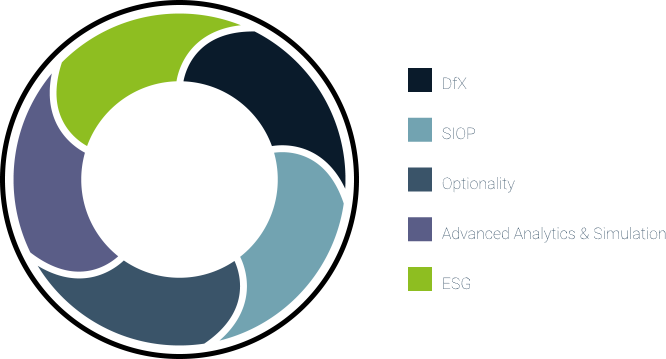
Design for Excellence
Leaders of an engineering or manufacturing company are usually well-versed in Design for Excellence (DfX). However, CEOs in industries as disparate as consumer goods and retail (design for preparation, design for service) and private equity have found that DfX is closely aligned with their company’s profitability and affects every multimillion-dollar decision.
Among the most important objectives for DfX is monitoring and controlling complexity. Reducing complexity improves communications, procurement, operations, logistics, and quality control across the end-to-end supply chain.
For example, reducing complexity at the SKU and component level improves inventory control by curbing obsolescence through the use of standard or identical parts, modules, or subsystems across multiple projects. It also increases the speed and agility of operations, while requiring fewer supplier tiers and making it easier to pivot with changing customer demands.
At a manufacturer of custom equipment for railways, engineering and operations rarely collaborated. As a result, work instructions from engineering would cover thousands of hours of production in a single step, making it difficult to track progress. Quality control had to wait until the last week of production, leading to major rework and delays. SGS Maine Pointe worked with engineering to refine work instructions, set up visual boards to track production status, added KPIs, and trained quality control to identify deficiencies early on. Machining operations gained 60 percent in efficiency; quality defects dropped 40 percent; and EBITDA increased 20 percent with a 2.33:1 ROI.
In the retail industry, DfX is an integral part of decisions about ways to organize shelf space, reduce the average service time, and maintain the balance between supply and demand, among others. From warehouse to virtual store front, DfX influences traffic, efficiency, customer relationships, and profits.
In addition, DfX is important for any automation initiative. If a process is bottlenecked and inefficient, automating it will not fix the underlying problem.
When you initiate DfX in your company, across enterprises and functions, you clarify the relationship of customer needs, accountability, and total costs to profitability. Even one decision—say, to redesign a standard part for improved manufacturability—touches every link in your supply chain.
As part of an integrated decision making strategy, DfX:
- Enhances core competencies
- Increases modularization of systems and commonality of components
- Enables timely, cost-effective, reliable sourcing, manufacturing, and assembly
- Avoids early obsolescence and the proliferation of customer options
- Increases efficiency and standardization throughout the end-to-end supply chain.
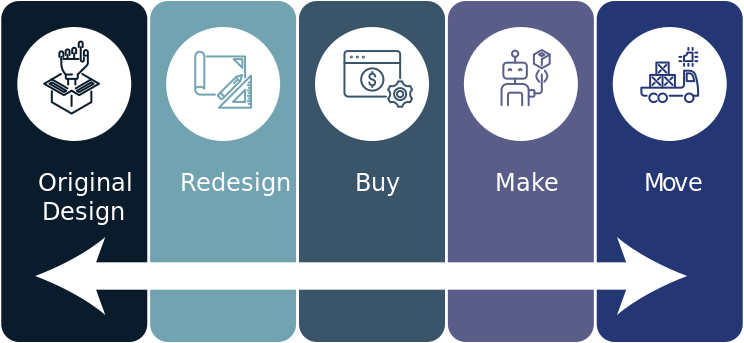
Sales, Inventory and Operation Planning
Sales, inventory, and operations planning (SIOP) is the basis for an integrated business plan that includes every link in the end-to-end supply chain from sourcing through delivery. If you need to control inventory, fix demand and supply imbalances, improve customer satisfaction through on time and in full (OTIF) production, and use capital more strategically, SIOP processes are the place to start.
As stated in the SGS Maine Pointe eBook, Sales & Operations Planning, SIOP requires “executive leadership (finance, marketing, sales, and supply operations) to act in pursuit of common goals, rather than in pursuit of an isolated functional goal such as sales revenue, cost-per-unit purchased or sold, or cost-per-mile transportation costs.”
In return, high-level SIOP, with a synchronized supply chain, gives C-level leaders the oversight they need to ensure free-flowing information between functions and subsidiaries and adherence to standard KPIs and metrics that align with company goals. Otherwise, the C-suite is in a constant state of fighting fires and struggling to understand the exact source of problems in time to fix them.
SGS Maine Pointe retooled SIOP for a company offering clean alternatives to industrial processes, establishing the strong KPIs and metrics needed to create a single, reliable source of data. A spend cube provided reliable data on purchases; a managerial dashboard improved compliance and tracking; and a customized playbook accelerated the adoption of sustainable SIOP practices. Further, by creating a clear separation of planning and execution—important for both DfX and SIOP initiatives--SGS Maine Pointe reduced the number of unplanned engineering changes from multiple times every day to zero and rescued important supplier relationships.
A SIOP that is synchronized with the end-to-end supply chain involves every function in gathering, evaluating, and applying data. It uses advanced data analytics, simulation, and predictive techniques, to account for risk, EBITDA, cash flow, sustainability, and value to customers and stakeholders, among other factors that influence C-level decision making. It provides the C-suite with visibility and control over procurement, operations, and logistics.

As part of an integrated decision making strategy, SIOP:
- Tracks compliance with goals and KPIs
- Increases accuracy of forecasting, provides reliable data for decision making, and helps to evaluate and manage change
- Ensures customer satisfaction by managing inventory and on-time, in-full (OTIF) production
- Improves resource planning, from available capital to workforce management.
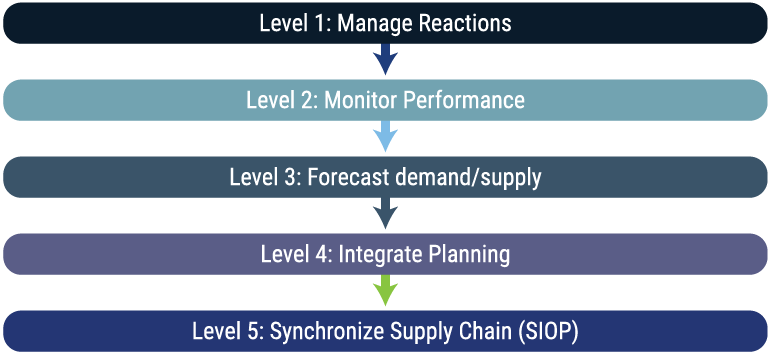
Optionality
Do you need to expand your footprint or would you be better off erecting new facilities in a new location?
If you choose a new location, where in the world would be best? What risks and benefits will the new location involve; for example, finding a capable work force, protecting intellectual property, or accessing customers or suppliers? If the location improves your access to suppliers, will it concentrate all your sources off-shore, where they are more vulnerable to logistics problems? Is it possible to find suppliers near-shore who are open to negotiation?
In the past, your C-level team may have made those decisions on a straight-forward cost/benefit basis. In these days of volatility and uncertainty in geopolitics, consumer trends, and even weather, C-suite decisions must encompass many more factors, including the downtime caused by any move, union labor costs, time to ROI, and availability of raw materials from the suppliers’ suppliers
Suppliers to a global manufacturer and developer of specialty polymers refused to respond to requests for proposals, creating a risk of shortages. SGS Maine Pointe built relationships with nontraditional sources in Europe, Mexico, Africa, and Turkey, replacing sources in Asia, and with domestic companies with fewer logistic issues. As a result, supply chain costs fell by 6 percent.
As described by Collin Ziemenek, Head of Industrial & Manufacturing Services at SGS Maine Pointe, “The C-suite uses capacity, geography, and supplier optionality to develop ‘what if’ scenarios that identify the best strategic options to meet company goals.”
In their simplest forms, capacity optionality considers whether to optimize or expand on current resources or to build or acquire new facilities; geographic optionality evaluates where to move, acquire, or build facilities in a new location or an existing location; and supplier optionality evaluates in-shore, off-shore, and on-shore opportunities for expanding the supplier base. These decisions require in-depth collection of data across the end-to-end supply chain and are evaluated against multiple criteria.
As part of an integrated decision making strategy, optionality:
- Reduces risks by ensuring suppliers can meet capacity demands and logistics constraints
- Leverages time, capacity, negotiation, and logistics considerations to meet company objectives
- Tests risks and opportunities against “what if” scenarios
- Takes all considerations into account—from security threats to natural disasters—when choosing geographic locations
- Establishes uniform criteria for evaluating and negotiating with suppliers.
Advance Analytics & Simulation
Real-time, data based decisions are the foundation for all improvements in the end-to-end supply chain, from tracing cash flow and automating manufacturing to meeting customer expectations. The chief impediments to real-time data based decisions include incomplete data locked into silos; unreliable data generated by inconsistent (or nonexistent) KPIs and metrics; and data that is simply outdated.
Therefore, to grasp the advantages of advanced analytics and simulation, the C-suite must first examine its data sources for consistency, timeliness, and thoroughness. Advanced analytics based on flawed data will merely perpetuate flaws, severely limiting the value of any decisions, whether related to supplier negotiations or automation technologies.
Reliable data is, in fact, one off-shoot of DfX, SIOP, optionality, and ESG, based on fundamental improvements in processes and people. In a recent interview, Nathaniel Powrie, Managing Director of Data Analytics at SGS Maine Pointe, stated: “By combining data from both humans and machines with advanced analytics and predictive insights, we can optimize decision-making in a near real-time manner. (Companies will realize) a host of benefits from having that real-time visibility into their network.”
Among other benefits, real-time visibility allows the construction of a digital twin of the end-to-end supply chain, a virtual representation that allows companies to uncover bottlenecks, foresee risks, and test out decisions before they are implemented in the real world. The digital twin market is expected to grow at over 42% CAGR in the next five to six years, reflecting the importance of this technology across every industry. The goal of the digital twin is to enable the C-suite to make decisions with confidence.
When a manufacturer of cable systems ran out of manufacturing and warehousing space, they turned to SGS Maine Pointe for a detailed analysis of the best location for a future expansion. Using network modeling, with a center of gravity analysis, the SGS Maine Pointe team recommended moving the distribution center to a location closer to customers and using the vacated space to double the manufacturing footprint. By combining those recommendations with SIOP practices, such as a daily schedule control (DSC), the team increased throughput 14 percent for an ROI of 5:1 in year one.
Interrelated Success Factors
As part of an integrated decision making strategy, the use of advanced analytics and simulation:
- Ensures that the C-suite bases decisions on timely, accurate, and complete information
- Enables the company to automate strategically
- Reveals opportunities for scale, cost reduction, improved quality, and competitive advantage
- Exposes bottlenecks and risks.
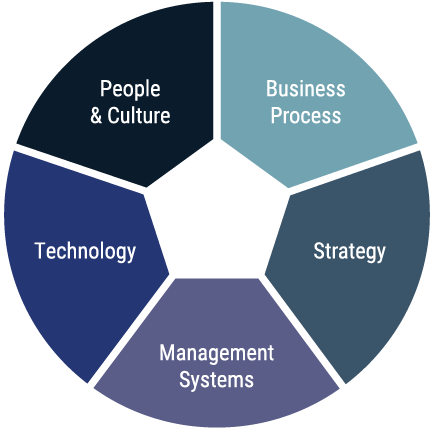
Environmental, Social, and Governance (ESG)
Every one of the practices and processes described previously influences and is influenced by environmental, social, and governance (ESG) issues. In some ways, ESG is the starting point of every decision-making strategy. It is the glue for collaboration between functions and subsidiaries, the impetus to shared values and information, and the reason that you can depend on the quality, timeliness, and completeness of the data you receive.
Because poor information about ESG itself and concerns about ROI are the biggest hurdles to ESG implementation, companies need metrics that track the ROI of each effort. Metrics not only build credibility, but verify a return on investment throughout the supply chain. Take, for example, these ESG initiatives:
- Reducing fuel consumption: Use supplier optionality to also bring sourcing closer to manufacturing
- Reducing packaging: Use Design for Excellence to save both money and the environment
- Engaging stockholders, customers, and communities: Use SIOP to simultaneously increase productivity and efficiency
- Determining the true cost and benefit of any ESG initiative: Use advanced analytics and simulation allow companies to evaluate ESG decisions against their effect on the end-to-end supply chain.
Purpose-driven companies have higher levels of collaboration and engagement and are better able to access reliable, timely data, the foundation of ESG, optionality, DfX, SIOP, and advanced analytics and simulation. When employees are trained in ESG, understand the business strategy, and have strong communication across the end-to-end supply chain, the ability to gather, use, and evaluate information soars. Diversity, equality, and inclusion (DEI) initiatives also have a proven correlation to improved employee retention, innovation, and overall performance of the company.
A manufacturer of simulators for the commercial aircraft industry merged with a similar company focused on military aircraft. The two companies had different approaches to collaboration, redundancy, tracking, and analysis. SGS Maine Pointe identified and mapped over 650 tasks in 19 work streams; developed a 5X5 cultural matrix to identify and define the company’s top five values; and used process mapping, value stream mapping, and straight negotiation to bring the two companies into sync. As a result, the company garnered an additional $8 million in savings from the merger, exceeding its own post-integration goals.
As part of an integrated decision making strategy, ESG:
- Engages employees, investors, and customers, directly benefitting the company with increased productivity, investment attraction, and sales
- Reveals opportunities to reduce costs across the supply chain; for example, in energy consumption, transportation, and waste reduction.
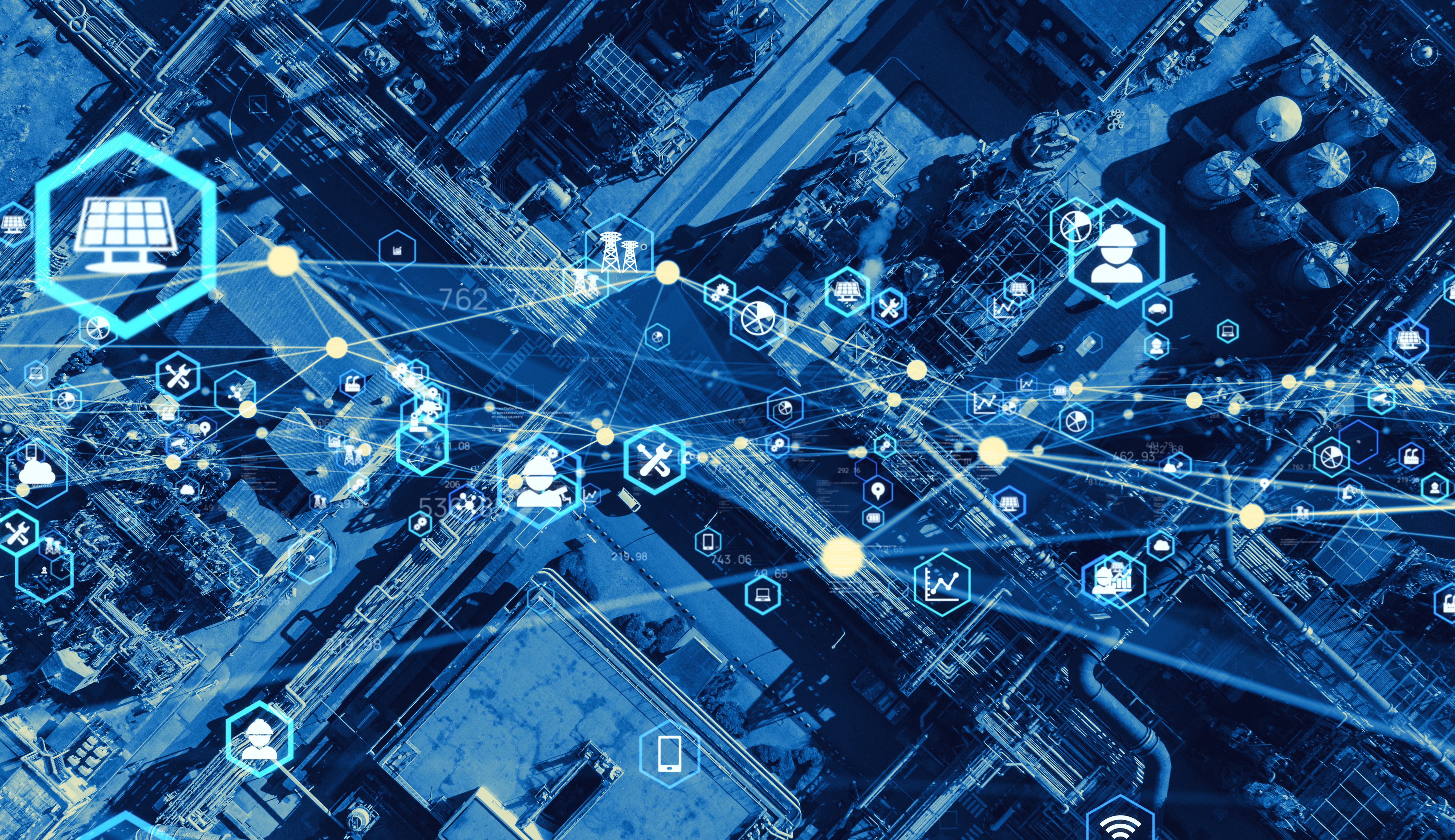
Conclusion
Applying DfX, SIOP, optionality, advanced analytics and simulation, and ESG as a cohesive strategy reveals and confirms the full value of any decision. This approach prevents gains at one end of your plan-buy-make-move supply chain from being offset by losses somewhere else. It addresses and resolves underlying issues, such as lack of collaboration between functions, single-source suppliers, unreliable data, imbalances between supply and demand, and inefficient processes.
By offering you a wider lens for decision making, SGS Maine Pointe penetrates silos; unleashes the full potential of your company; uncovers sustainable savings; ensures that the value gained is justified by the ROI; and drives improvements in EBITDA, cash, growth, and resilience.