Navigating the Modern Manufacturing Maze: Solutions to the Supply Chain Crisis
Supply Chain Problems in Manufacturing: Causes and Cures
Manufacturers are facing some difficult supply chain problems: labor shortages, unprecedented advances in technology, economic turbulence that makes it hard to balance supply and demand, and shifts in supply chains that raise complex questions, such as whether increasing prices, adding technology, or reshoring is the best response.
Challenge 1: labor shortages
While better benefits and higher pay may tempt workers, over 2 million manufacturing jobs will still be unfilled in 2030, according to industry estimates. Companies are therefore well-advised to take approaches that do not depend on finding more bodies, including the following:
- Network and footprint optimization ensure that resources are allocated efficiently. By minimizing waste, reducing bottlenecks, and streamlining processes, manufacturers can make the most of their available workforce. A supply chain analysis can also indicate where labor shortages are greatest and have the most impact.
- Implementing automation and advanced technologies such as robotics, AI-driven analytics, and IoT devices is already alleviating the need for a large workforce in manufacturing. However, those solutions also increase the need for skilled technical labor and the devices themselves may be in short supply.
- Close collaboration with suppliers, with timely deliveries of raw materials and components, ensures that production lines continue to run without interruptions due to shortages.
- Both balancing supply and demand and employing Lean manufacturing principles reduce the need for excess labor and increase overall efficiency.
- Cross-training makes the existing workforce more versatile and able to fill gaps in specific areas.
- In cases where certain tasks or processes are not feasible in-house, manufacturers can consider outsourcing or forming partnerships with other companies that specialize in those areas.
- Proper inventory management ensures that production continues at the right pace without creating stockouts or excess, reducing pressure on the workforce.
- An optimized supply chain can lead to reduced lead times, which can help manufacturers respond more swiftly to changes in demand and help prevent sudden shifts in production.
Challenge 2: advances in technology
Predictive analytics, virtual reality, IoT sensors, robots, computer vision, and virtual reality: the list of devices meant for manufacturing is rapidly lengthening. It holds the promise of reducing costs, improving quality and speed, and compensating for labor shortages, but it also creates upheaval.
Optimizing the supply chain can facilitate a company’s ability to adopt new technologies with less disruption. By looking at and optimizing the entire plan-make-buy-move supply chain, companies can:
- Ensure they acquire only those technologies they truly need after the supply chain is optimized.
- Identify bottlenecks and inefficiencies in their current production processes, allowing for smoother integration of new technologies and less downtime during the transition.
- Ensure they have accurate data about processes, inventory levels, and customer demands so that technology is set up properly.
- Identify potential disruptions and develop contingency plans in advance.
- Strengthen their relationships with technology suppliers to better access the expertise and resources needed for adopting new technologies.
- Have a change management process and a roadmap for changes in place, with clear roles and responsibilities.
Choosing the right technology from the right manufacturer requires due diligence and, preferably, a due diligence playbook that can be followed each time a technology is considered. That playbook would cover investigations into the reliability of the technology and various suppliers, costs, and long-term benefits.
Challenge 3: economic turmoil
Globalization exposes manufacturers to economic risks like supply disruptions and supplier instability; changing export regulations and tariffs; differences in approach to sustainability and ethics; and currency fluctuations. Through supply chain optimization, companies gain a more resilient supply chain.
Advanced analytics and supply chain modeling identify potential vulnerabilities and enable data-based decision making on ways to avoid or minimize them. The data might indicate needed changes in sourcing, transportation, and production that are more cost-effective. By minimizing costs, manufacturers can remain competitive even in challenging economic environments.
Globalization increases the competition for customers, raw materials, and technology from “purely local” to worldwide. The workforce also varies from country to country, with differences not only in expected wages but in skill, availability, and attitudes. Companies need optionality, SIOP, network optimization, and advanced analytics but they also need clear communication about goals, KPIs, and standards to operate in a global environment.
Challenge 4: supply chain shifts
Labor shortages, technology, and economic turmoil all affect the manufacturing supply chain. They raise complex questions including:
- How vulnerable will manufacturing become to cyber attacks as it adds technology? How can companies secure a workforce skilled enough to use, maintain, and fix that technology?
- Is it time to build, expand, or move facilities and should those facilities be closer to suppliers or to customers?
- What forms of transportation will reduce carbon emissions, make the supply chain more resilient, and service customers at the speed they expect? Would it be more or less economical to use 3PL or 4PL suppliers?
- What mergers or acquisitions will add value, such as bringing needed capabilities in-house or reaching new customers?
- Would reshoring or more supplier optionality give us better control over sourcing?
- With shortages in raw materials and labor, should we increase our outsourcing and let our suppliers handle the problem?
While the answers vary for every company, the process of getting those answers is the same and begins with supply chain visibility. The main strategies to gain visibility include well-defined objectives and KPIs, trustworthy data gained through collaboration and communication, real-time monitoring, data analytics, and supplier relationship management. However, a company also needs the right supply chain visualization tools and technologies.
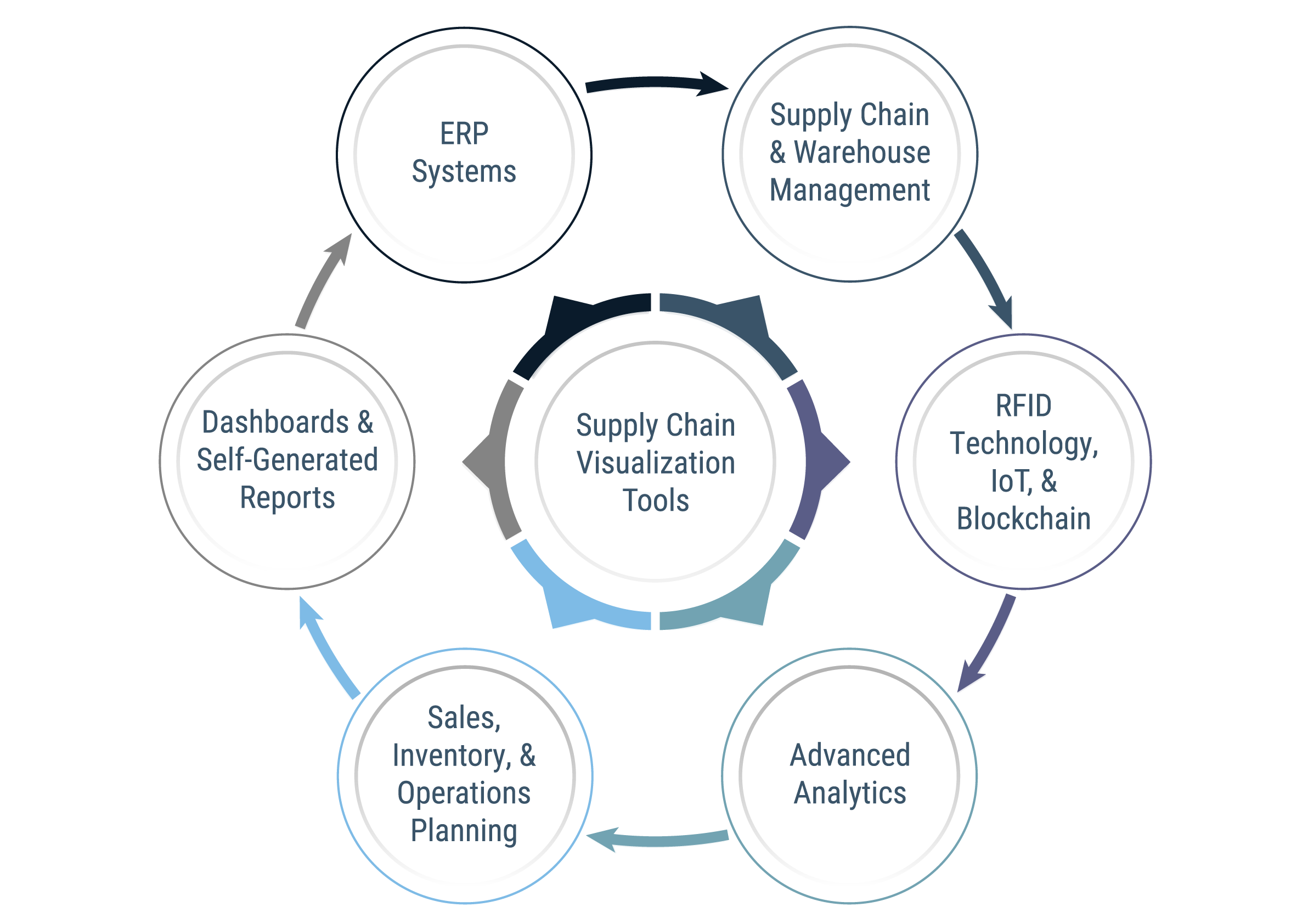
ERP systems integrate various aspects of business operations and enable real-time tracking of inventory levels, production progress, and order statuses. Supply chain management (SCM), warehouse management, and manufacturing executive systems help optimize demand planning, inventory levels, order fulfillment, and distribution; they capture real-time data on manufacturing activities.
RFID technology uses tags and readers to track and identify items as they move through the supply chain. IoT devices and sensors gather data on equipment health, status, and performance. Blockchain offers a secure and transparent way to record and share supply chain transactions.
Analytics tools process the vast amount of data collected from various sources within the supply chain. They can help identify trends, patterns, and areas for improvement. Sales, inventory, and operations planning (SIOP) processes ensure supply and demand are synchronized. Real-time dashboards and self-generated reports enable quick decision-making by presenting information in an easily understandable format.
Supply Chain Optimization: The Long-Term View
When it comes to optimizing the supply chain, manufacturing companies may lack specialized knowledge, experience, and objectivity. For example, increasing competition for a legacy supplier through optionality might be objectively sound, but the company may find it nerve-wracking to loosen those familiar ties, and the procurement department may have never needed to locate, evaluate, or negotiate with suppliers. Companies may have also lost contact with best practices in the industry or be so used to certain inefficiencies that they no longer see them or be able to consider alternatives.
However, labor shortages, technology change, economic turbulence, and supply chain vulnerabilities are not going to disappear. The more interconnected the world becomes, through trade or technology, the more important a resilient supply chain becomes to the health of every manufacturing company.
Manufacturing by the numbers
World |
US |
|
Rate of Digitization Per 10,000 Employees | 322 Robots | 117 Robots |
Percent of Workforce Employed | 14% | 9% |
Unfilled Manufacturing Jobs | 8 Million | 2.1 Million |
Annual Growth of Market | 3.5% | 3.05% |
Contribute to GDP | 16% | 12% |